PCB Design Services: Elevating Electronic Design with Expertise
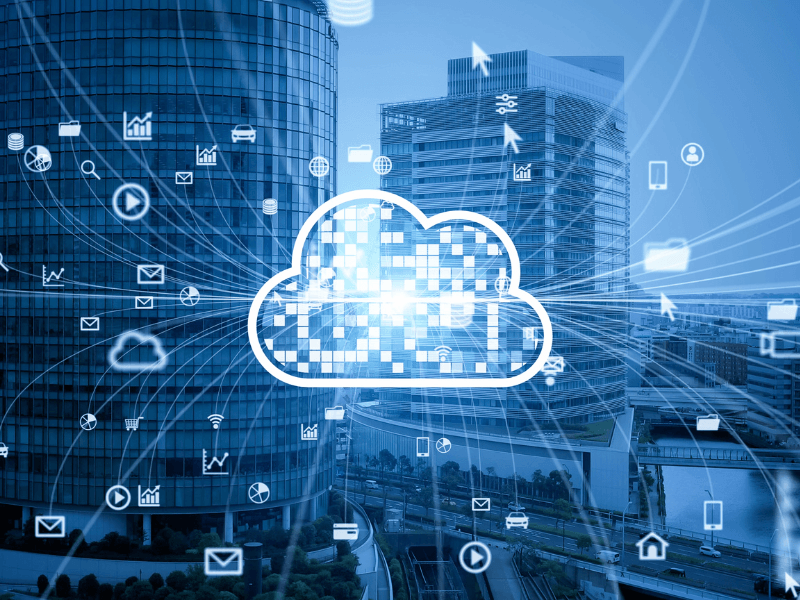
In today’s electronics-driven environment—from consumer gadgets and industrial automation to aerospace controls—high-quality PCB design services are essential. A well-engineered PCB ensures not only functionality but also reliability, manufacturability, thermal efficiency, and signal integrity. Wagner Engineering USA, a boutique U.S.-based firm founded in 2025, provides comprehensive PCB design services that blend technical excellence with cross-domain know-how—all the way from schematic capture to prototype-to-production handoff.
1. The Value of Expert PCB Design Services
PcBs are much more than printed copper; they are complex platforms coordinating power delivery, control logic, signal paths, mechanical fit, and manufacturing considerations. Choosing a professional PCB design service offers the following benefits:
-
Signal integrity and noise management: Precise routing for differential pairs and impedance control to maintain high-speed performance.
-
Thermal reliability: Thermal vias, copper planes, and component placement strategies to dissipate heat effectively.
-
Manufacturability: Designs compatible with real-world fabrication and assembly processes—to reduce errors and schedule delays.
-
Regulatory compliance: EMC, safety, and environmental standards embedded into the layout.
-
Iterative validation: Through cross-functional collaboration and hands-on iteration, ensuring first-pass build success.
These services ensure that your design moves confidently from concept to working hardware without unexpected iterations.
2. Wagner’s PCB Design Expertise
A. Requirements Gathering and Feasibility
Every project begins with a detail-oriented kickoff: defining electrical specs, mechanical constraints, signal types, regulatory needs, and board dimensions. Wagner’s team collaborates closely with clients to align these inputs, minimizing surprises when the layout begins.
B. Schematic Capture & Footprint Validation
Although centered on layout, Wagner’s PCB design services seamlessly integrate with schematic creation. They verify netlists, ensure footprints and 3D models match components, and guard against errors that could derail assembly downstream.
C. Component Placement
Effective layout begins with intelligent part placement. Wagner factors in:
-
Signal flow and trace lengths
-
Ground and power plane accessibility
-
Thermal dissipation and heat sink proximity
-
Ease of assembly and test
-
Size and mechanical considerations
This thoughtful placement sets the stage for high-quality board routing.
D. Routing & Layer Strategy
Routing includes both power paths and signal traces—especially critical in high-speed designs. Wagner engineers optimize:
-
Controlled impedance for differential pairs (USB, Ethernet, PCIe, DDR)
-
Crosstalk reduction through layering and spacing
-
Balanced trace lengths and matched pairs for timing-sensitive signals
-
Multi-layer board stacking for optimized plane distribution
E. Signal Integrity & EMI Management
High-frequency signals can be disrupted by reflections or emissions. Wagner’s layout services integrate controlled impedance and differential routing, along with shielding, via placement, ground stitching, and strategic trace geometry to mitigate EMI and EMI within tolerance.
F. Power Delivery & Thermal Considerations
Stable power distribution is essential. Wagner’s design includes:
-
Isolation of analog, digital, and power domains
-
Copper pours and planes for consistent current flow
-
Thermal vias & spreads to dissipate heat
-
Placement of heat-generating components to optimize airflow
These techniques contribute to smooth electrical operation and thermal stability.
G. Design for Manufacturability (DFM) Review
Fewer manufacturing surprises equals faster time-to-market. Wagner performs rigorous DFM checks—reviewing via sizes, panelization, component spacing, test pad access, and fabrication constraints—ensuring the layout aligns with industry-standard vendor capabilities.
H. Prototyping & Hands-On Validation
Wagner supports prototype assembly, solder bridging checks, continuity tests, and initial bring-up testing. Early validation avoids common pitfalls and ensures the PCB functions in hardware before moving to production.
I. Production Outputs & Documentation
Designers deliver full manufacturing outputs (Gerber, IPC-2581, ODB++, drill files), BOMs, pick-and-place diagrams, assembly drawings, 3D previews, and thermal reports. This documentation powers fabrication, assembly lines, and internal reviews.
J. Post-Production Support
Finished hardware often requires design iteration—whether due to minor signal challenges, thermal tweaks, or value engineering. Wagner provides responsive update cycles, lifecycle support, and assistance with future design variants.
3. Application Use Cases and Industry Experience
Consumer Electronics
Wearables, IoT sensors, and portable devices require miniaturized, thermally-efficient, and RF-friendly PCB solutions—precise design that Wagner excels in.
Industrial Controls & Automation
Led by robust signal and power integrity, industrial PCBs must withstand harsh environments. Wagner designs boards optimized for thermal resilience, EMI robustness, and manufacturability.
High-Speed Digital Systems
PCBs for high-speed communications, data acquisition, and compute systems demand exact trace lengths, impedance control, and crosstalk mitigation. Wagner’s layout practices support these domains flawlessly.
Embedded Control Logic
From motor control to sensor systems, reliable power domains and isolation between analog, digital, and wireless components are paramount in embedded layouts.
Medical/Industrial Safety Devices
Strict standards apply to medical hardware. Boards require controlled impedance, safety spacing, thermal compliance, and meticulous documentation—areas where Wagner excels.
4. Technology Platform & Toolchain
Wagner leverages industry-standard PCB tools and design strategies:
-
EDA Software: Altium Designer, Cadence Allegro, Mentor PADS/Xpedition
-
Simulation: Signal/path integrity, electromagnetic interference, thermal analysis
-
3D Integration: Mechanical clearance and enclosure fit validation
-
Manufacturing Standards: IPC, UL, RoHS/REACH compliance
-
Prototyping Tools: In-house test jigs, signal analyzers, and assembly benches
Advanced toolchains enable precision, repeatability, and high reliability for board designs.
5. What Sets Wagner Engineering Apart
U.S.-Based Collaboration
Designers located locally—facilitating real-time interaction, rapid decision-making, and secure IP handling under NDA.
Cross-Discipline Synergy
Integrating PCB layout with firmware, embedded software, and cloud connectivity provides consistent system-level performance across domains.
Holistic Quality Assurance
Skillful layering of SI, EMI/thermal simulation, and DFM reviews result in boards that are robust both electrically and mechanically.
Scalable Support
From a single-layout prototype to multi-board system designs, Wagner scales services to fit diverse project complexities and timelines.
Long-Term Partnership
They provide iterative lifecycle support for product upgrades, BOM changes, and design adaptations—lowering the total cost across product generations.
6. Typical Engagement Workflow
-
Project Initiation
Gather datasheets, mechanical info, schematic designs, manufacturing targets, and environmental requirements. -
Specification & Planning
Define layer count, impedance targets, material budgets, and schedule timelines. -
Component & Footprint Verification
Validate all footprints, 3D models, and library parts against mechanical enclosures. -
Placement Strategy
Perform iterative review cycles focusing on signal flow, power zones, and manufacturability. -
Routing & Signal Optimization
Execute controlled impedance traces, layer transitions, and EMI shielding. -
Review & Compliance Testing
Run DRC, SI/EMI simulation, thermal analysis, and manufacturability audits. -
Prototype Manufacturing & Testing
Coordinate board fabrication, assembly, bring-up testing, and validation labs. -
Production Support
Assist vendors, tune panels, optimize BOM cost, and produce final documentation. -
Maintenance & Revision Cycles
Implement RPM updates, footprint replacements, and design variant adaptations.
7. Measuring Success
Design success is judged through:
-
First-time-right prototype builds with negligible rework
-
Electrical performance metrics within tolerance thresholds
-
Low manufacturing rejects thanks to optimized DFM
-
Thermal stability under operational load
-
Production cost savings from optimized layout and vendor collaboration
Wagner’s collaboration ensures your design achieves these milestones efficiently.
8. Common Challenges & Wagner’s Solutions
-
High-speed trace mismatch → They apply impedance control and length matching tools.
-
Thermal hotspots → Addressed via copper pours, heat pipes, and strategic placement.
-
EMI concerns → Managed via proper layer stack-ups, shielding, and ground stitching.
-
Design-change ripples → Minimized through modular design and comprehensive documentation.
-
Assembly issues → Avoided through test pads, panelization design, and accessible footprints.
Each challenge is met with experience-backed solutions ensuring performance and reliability.
9. Engagement Models & Timeline
Wagner tailors delivery based on project need:
-
Fixed-price prototype builds for short schedules or low volume
-
Hourly or retainer contracts for on-demand revision cycles
-
Embedded design support for long-term product families
Typical durations range from 4 to 8 weeks for prototype boards and 8 to 16 weeks for complex multilayer designs.
10. Why High-Quality PCB Layout Matters
In fast-track electronics development, design flaws are some of the costliest mistakes. Professional PCB layout services reduce risk by eliminating signal defects, production delays, and quality issues—translating to faster time-to-market, lower fabrication cost, and scalable manufacturing readiness.
When precision, compliance, and product success matter, Wagner Engineering USA delivers PCB design services that go far beyond routing—they deliver reliability, strategic insight, and sustainable hardware development.
Effective PCB design services aren’t just about connecting pins—they’re about harmonizing electrical, mechanical, thermal, and manufacturing needs into unified, production-ready boards. With Wagner Engineering USA’s comprehensive approach—blending deep layout expertise, embedded systems insight, and full documentation—they elevate your PCB from prototype to market with confidence.
Whether your board is destined for performance-critical industrial systems, compact IoT modules, or safety-reliant medical devices, Wagner’s PCB design services ensure your hardware platform performs as intended—from schematic to shipment.
- Art
- Causes
- Crafts
- Dance
- Drinks
- Film
- Fitness
- Food
- Juegos
- Gardening
- Health
- Home
- Literature
- Music
- Networking
- Other
- Party
- Religion
- Shopping
- Sports
- Theater
- Wellness
